Residual stress in automotive powertrain components
Lead Researcher: Sina Kianfar
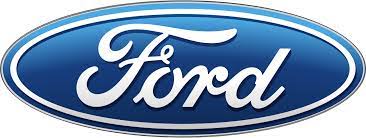
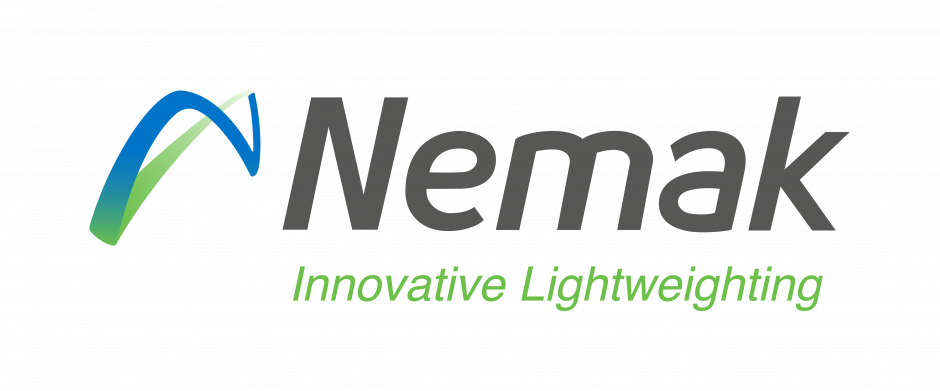
Next generation automotive engines demand advanced manufacturing technologies to meet efficiency mandates regarding energy conservation and emission reduction. This is commonly achieved by reducing weight and/or increasing the operating loads and pressure of the internal combustion (IC) engine. The majority of the weight reduction efforts have been focused on replacing the heavy ferrous alloys with lightweight aluminum (Al) alloys. However, the applicability of Al alloys for powertrain applications, such as engine blocks, is limited due to several factors, including an insufficient high-temperature strength and wear resistance. Therefore, cast iron (Fe) cylinder liners are extensively used to protect the Al cylinder wall from excessive wear. However, during the manufacturing of cast Al engine blocks with Fe liners, the mismatch of thermal expansion/contraction coefficients between the Al cylinder wall and Fe liners results in the development of high residual strains/stresses. This evolution of residual stress can surpass the strength of the currently used alloys and can lead to the distortion and/or premature failure of the engine block. Consequently, automobile original equipment manufacturers (OEMs) must incur enormous expenses for recalling and maintaining the failed products. Therefore, it is required to evaluate the residual stress formation during the engine block manufacturing (i.e., casting and heat treatment processes). An in-depth understanding of the manufacturing process effects on the residual stress can assist to improve the engine block’s durability and increase vehicles’ fuel efficiency, reducing their carbon footprint. This study aims to conduct comprehensive numerical and experimental investigations to develop a fundamental understanding of the evolution of residual stresses following current-day manufacturing innovations for the production of cast Al engine blocks. This further can lead to facilitate the design and manufacturing of the next generation powertrains with mitigated residual stresses.
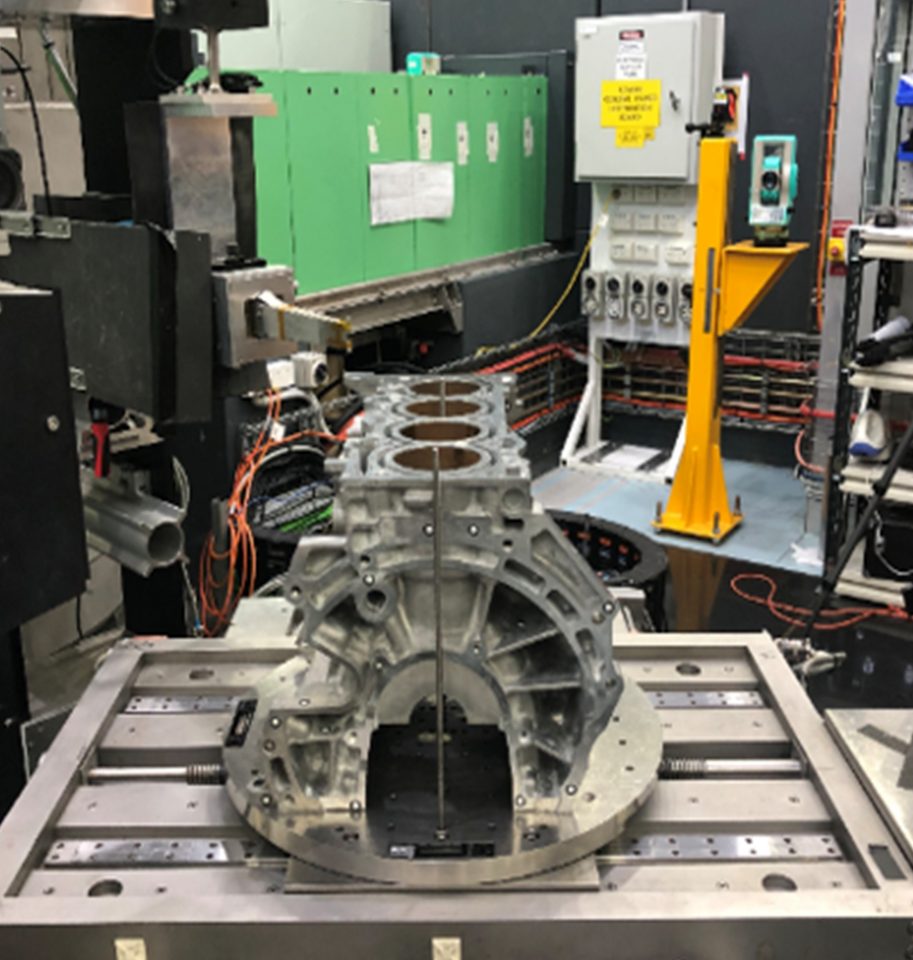
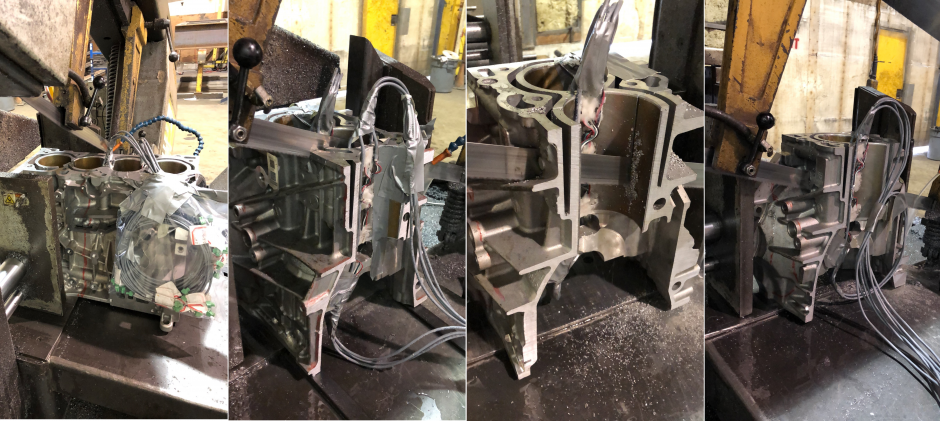
Nowadays, numerical modelling, employing finite element methods (FEM), has become essential for reducing the time-consuming prototyping stages. Correspondingly, advanced FEM techniques are viable tools for stress analyses in manufacturing processes, including casting and heat treating. In this research, a numerical model in an ANSYS commercial package was developed to assess the evolution of residual stresses during the casting and subsequent heat treatment processes. Due to the engine block’s complex geometry, which leads to complicated residual stress profiles, the simulation was initially conducted on a simplified standard geometry (i.e., stress-lattice castings in the as-cast, T4, and T6 heat-treated state) to determine the proper modelling and process parameters. Then, the casting and heat treatment processes of an inline-6 precision sand-cast (i6 PSC) engine block, produced by Nemak Canada, and an i4 high-pressure die-cast (HPDC) engine block, produced by Ford Motor Co., were simulated. Finally, experimental procedures, including, but not limited to, residual stress characterization utilizing a neutron diffraction technique, were employed to test and verify the FE model. Overall, this study’s outcomes will assist OEMs in optimizing the manufacturing processes of engine blocks with diminished residual stresses, leading to reduced cracking and distortion. Furthermore, reducing the residual stress results in greater magnitudes of engine block’s available strength, which allows the automotive industry to increase the combustion process’s temperature/pressure, and therefore, boost the IC engines’ efficiency.
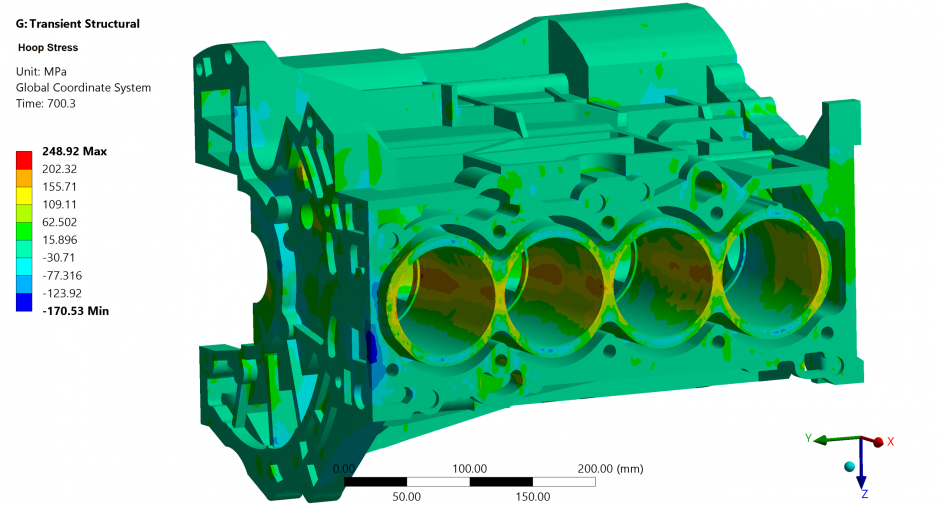
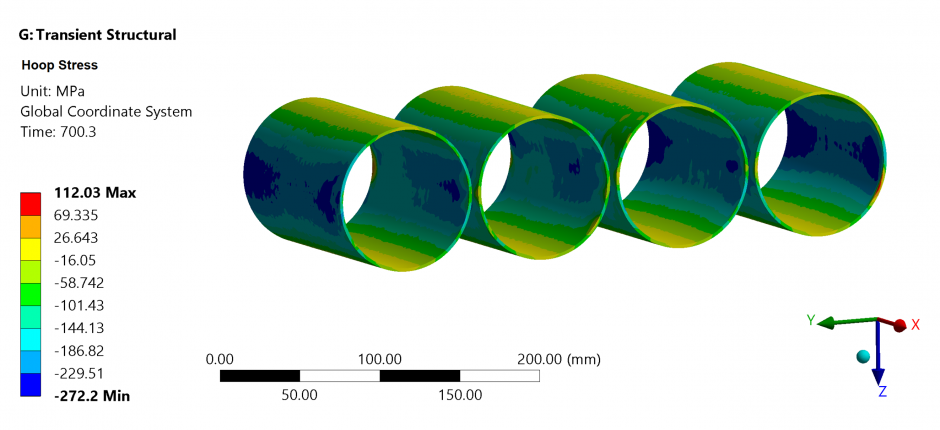
Publication
Kianfar, S., Aghaie, E., Stroh, J., Sediako, D., & Tjong, J. (2021). Residual stress, microstructure, and mechanical properties analysis of HPDC aluminum engine block with cast-in iron liners. Materials Today Communications, 26, 101814.
Sediako, D., Stroh, J., & Kianfar, S. (2021). Residual Stress in Automotive Powertrains: Methods and Analyses. In Materials Science Forum (Vol. 1016, pp. 1291-1298). Trans Tech Publications Ltd.
Kianfar, S., Stroh, J., Bahramian, N., Sediako, D., Lombardi, A., Byczynski, G., … & Paradowska, A. (2021). Residual Stress Prediction in the Casting Process of Automotive Powertrain Components. In Light Metals 2021 (pp. 858-864). Springer, Cham.
Residual stress in friction stir welding
Lead Researcher: Nicholas Sabry
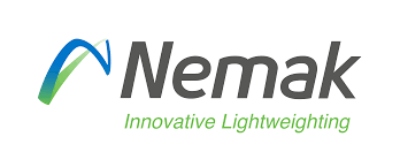
With the growing demand for increased battery capacity and performance, a congruent challenge for adequate cooling has developed. Nemak, a global automotive parts manufacture, decided advanced cooling requires unique cooling structures in battery trays. Nemak uses the High-Pressure Die Casting (HPDC) process to manufacture the internal cooling structures with A356 material to create these battery trays. The HPDC process, in this case, cannot cast both internal and external structures. Therefore, to complete the assembly, a Friction Stir Welding (FSW) process is used to join the internal casted cooling structure to the external structure made of 6061 Al sheet material.
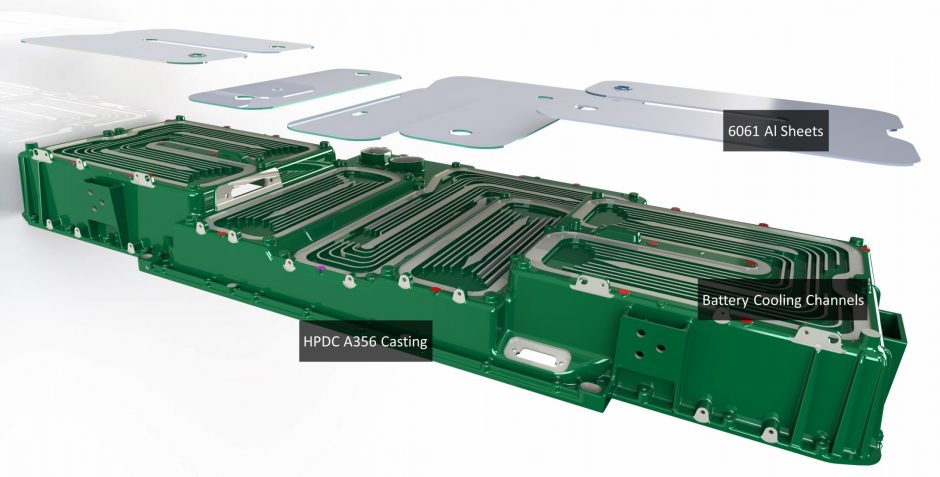
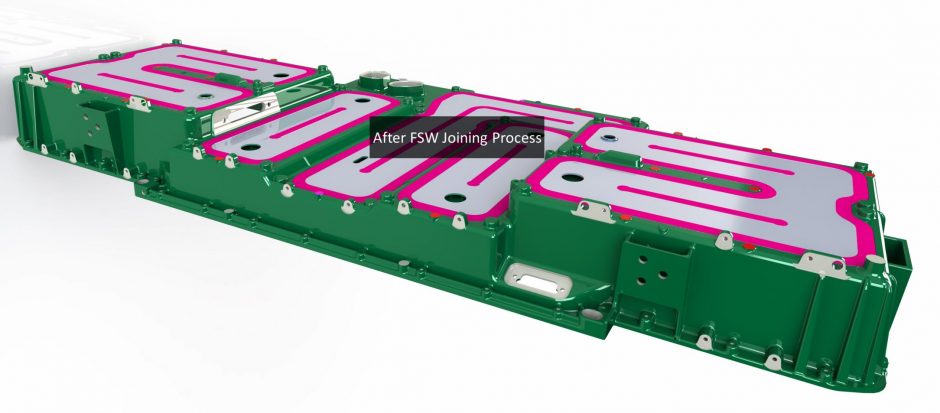
This project investigates the residual strain/stress accumulation that occurs after the FSW operation in the production of the battery trays that will be used in the next generation of hybrid and electric vehicles. The FSW joining process causes the battery tray to achieve relatively high temperatures while welding two different materials A356 and 6061 Al, producing significant changes to the microstructure of the material around the welded zone:
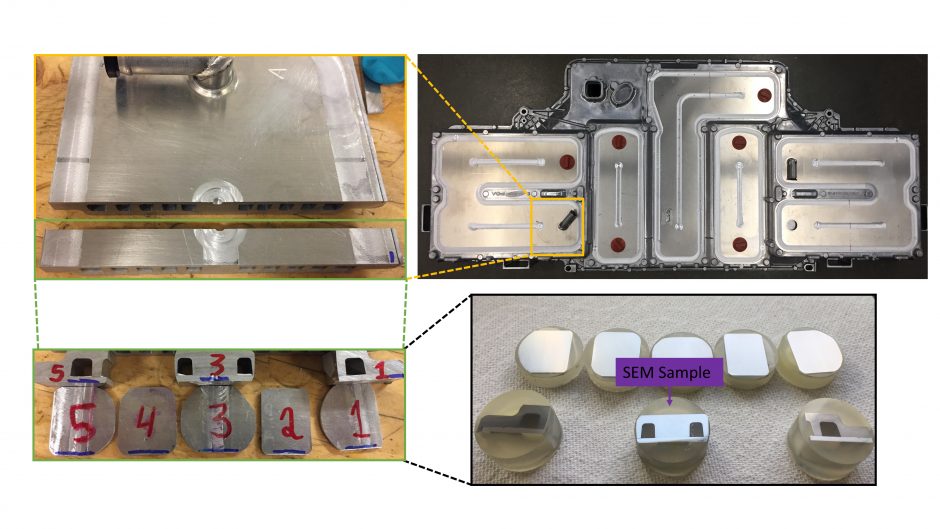
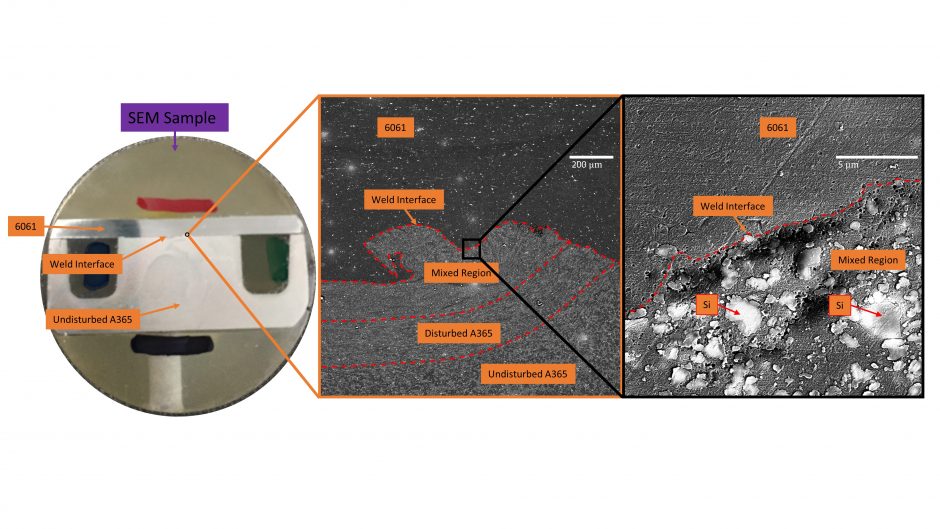
The FSW process also causes residual stress evolution, leading to distortion of the tray. The distortion is so significant that the tray cannot be attached to the vehicle. Therefore, post-processing straightening methods must be applied, burnishing or coning processes, adding to the production cost. It is unclear how different welding conditions and the post-processing techniques (straightening techniques) affect the induced stress; therefore, the strain in the deformed as-welded state, burnished, and conied battery trays are determined and compared. Neutron Diffraction and Strain Gauge techniques are employed to measure the strains across the friction stir welded seam in three different battery trays for this project.
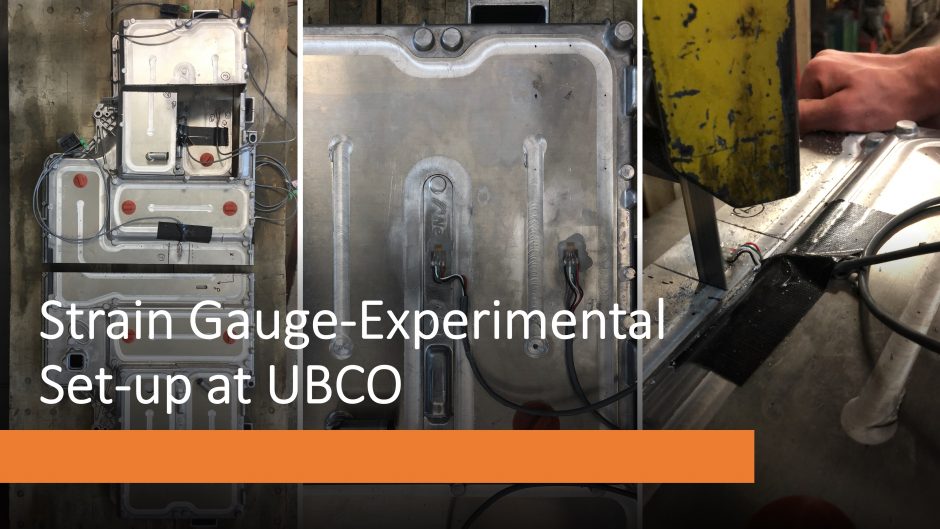
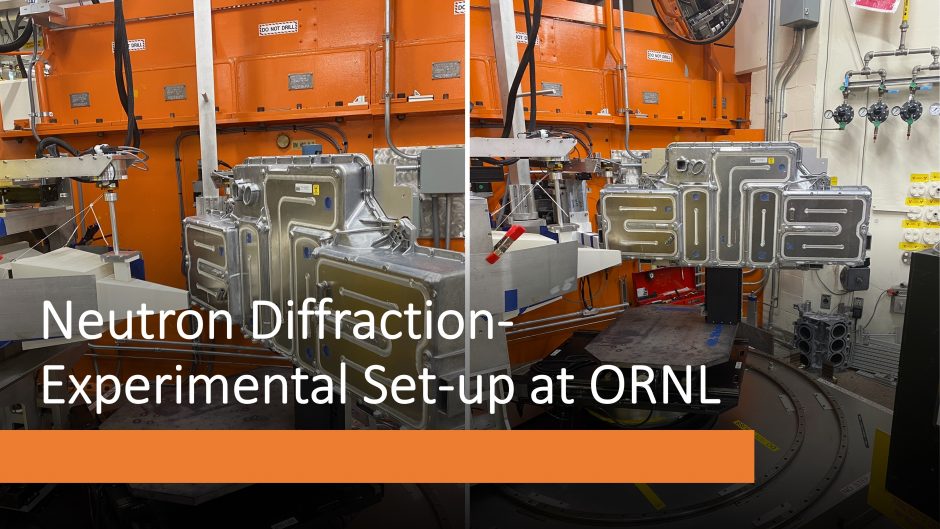
Measuring the strain across the welded seam in three orthogonal orientations provides valuable information on the magnitude of stress formation in three areas of interest, specifically the heat-affected zone, thermo-mechanically affected and the weld zone in the battery trays.
More information about friction stir welding on battery tray can be found in the following.
Publication:
N. Sabry*, D. Sediako, A. Lombardi, G. Byczynski, (Nemak Global Team), “Effect of Friction Stir Welding Operations and Post Processing Straightening on the Residual Stress of Electric Vehicle Battery Trays”, Materials Science and Engineering A, in preparation